全球拉响能源危机的警报,节能减排成为汽车行业刻不容缓的使命。在这一背景下,电动化已是大势所趋。在电池能量密度没有大范围突破的情况下,整车重量的降低能有效提升电动车续驶里程,直接促进电动车的普及度。
电动车轻量化领域,一个普遍的观点是,实现电动车轻量化有三大途径,即轻量化材料应用、结构优化设计和先进制备工艺。电动化时代下,材料供应商承担起更重要的角色,轻量化已不仅仅是锦上添花而已,而是企业面临的前所未有的挑战。近期,本刊记者采访到阿朗新科中国技术服务和应用开发经理冯伟军和阿朗新科中国技术经理陈民杰博士,听听他们讲述阿朗新科如何通过三大途径赋能电动车轻量化,以及公司在挑战与机遇并存的行业新常态中如何立足。
01
轻量化材料应用——车用橡胶的创新
阿朗新科的优势领域在于合成橡胶,公司对于自身的立足之本理解透彻。陈民杰指出,更轻、更环保的理念对车用橡胶材料提出了更高的要求。目前,阿朗新科橡胶材料已多方位应用于电动汽车零部件的制造,包括轮胎和其它非轮胎汽车零部件。比如三元乙丙橡胶(EPDM),氢化丁腈橡胶(HNBR),乙烯-醋酸乙烯酯橡胶(EVM),丁腈橡胶(NBR),以及氯丁橡胶(CR)。

除了动力电池、车身、底盘等大部件外,轻量化其实涉及到电动汽车的方方面面。看似不起眼的车用橡胶,也起到了不容忽视的作用。例如,传统的由硫化胶生产的汽车密封条,其密度一般在1.25g/cm3左右。而新型的基于EPDM生产的热塑性动态硫化橡胶(TPV),也可以用来生产汽车密封条,其密度只有0.95g/cm3左右,TPV密封条减重可达20%以上。阿朗新科还有一款生物基EPDM,采用可再生的甘蔗材料制得,可以用来生产TPV,符合环保的理念。此外,TPV密封条的断面更小,也有利于汽车的轻量化。
另一项能够体现阿朗新科创新力的则是对汽车电线材料的活用。汽车电线是汽车电路的网络主体,其绝缘层一般采用PVC材料。随着汽车电气化的发展,电子控制技术的普遍应用,电气件越来越多,电线也会越来越多,线束也就变得越来越重。PVC材料有一定的阻燃效果,但是PVC电线在燃烧时会有浓黑的烟雾和有毒的盐酸气体,不是环保的阻燃材料。阿朗新科有一款乙烯-醋酸乙烯酯橡胶(EVM),可以作为电线的绝缘材料,替代PVC。EVM硫化橡胶的比重1.2g/cm3,小于PVC绝缘材料(1.5g/cm3)。更具前瞻性的是,EVM是一种无卤阻燃材料,可以生产无卤阻燃电线,更加环保。
02
结构优化——轮胎材料的轻量化设计
“与传统汽车相比,电动汽车所采用的电气化动力系统会带来超高的轮胎扭矩和极速性能,因而要求橡胶材料有更加优异的强度和韧性。”冯伟军解释道。
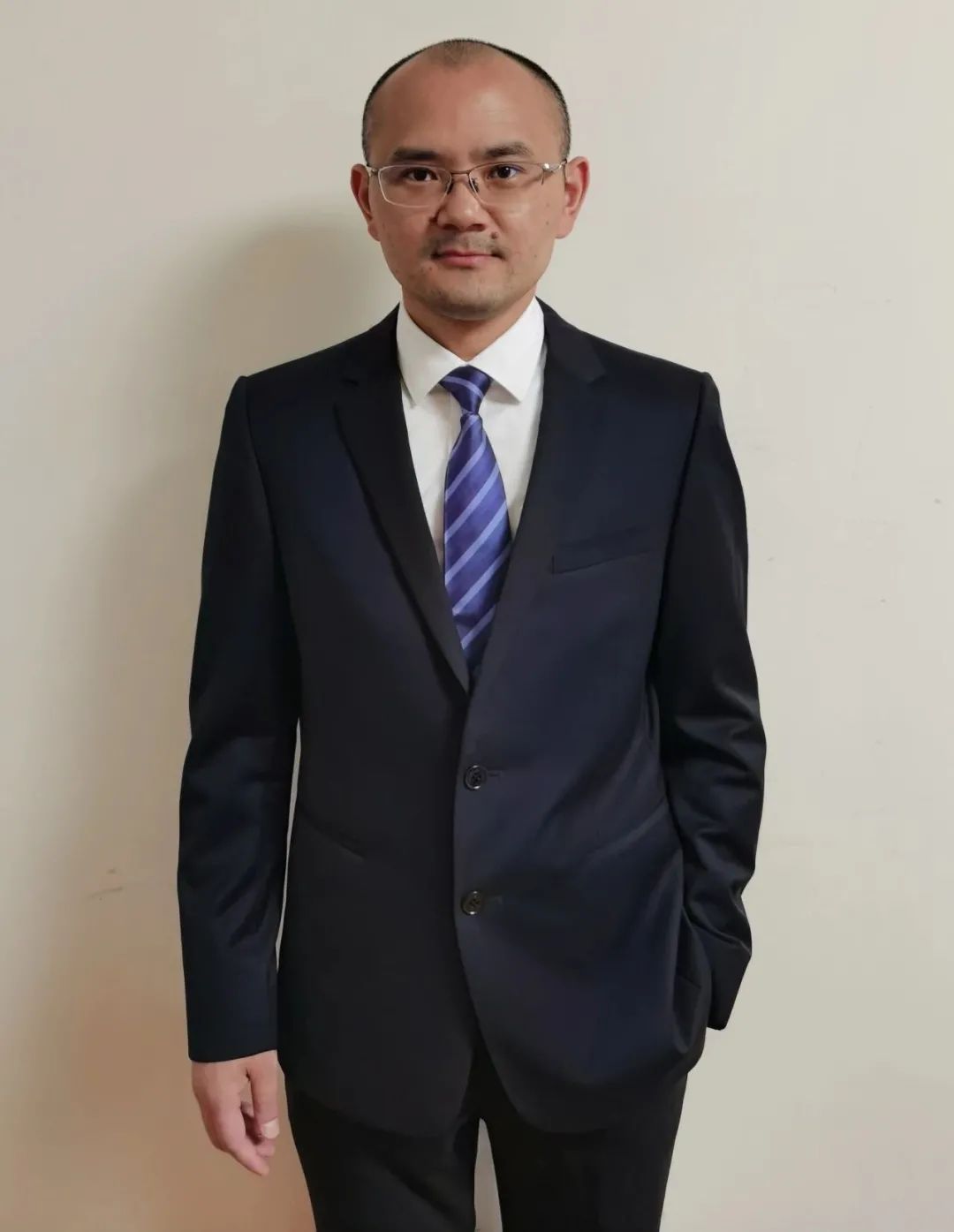
阿朗新科中国技术服务和应用开发经理冯伟军
电动化时代,整车的动力不再局限于发动机的性能,电机数目的叠加或功率增加使得普通电动车也具备优异的运动性。因此,轮胎必须进一步提升干抓,湿抓性能和操控性能。作为轮胎胎面主要合成胶的溶聚丁苯,需要进一步的官能化改性以提高轮胎抓地性能。而作为胎侧主要合成胶的顺丁橡胶将会主要关注高新能钕系顺丁(NdBR)以提高模量的同时降低生热。而对轮胎更优异的耐久性需求,必然要求轮胎气密层的丁基胶性能更佳。
阿朗新科对电动汽车轮胎的结构优化体现在其优异的轻量化轮胎材料解决方案。首先,通过使用缺气保用轮胎,从整车设计上可去除备胎轮辋总成,为汽车带来近30kg的减重,并在后备箱留有更大空间以备电池的安装和排布。其中稀土顺丁橡胶/NdBR因其优异的低生热和高模量,因而在缺气保用轮胎的胎侧支撑胶中应用是必不可少的。
其次,低滚阻是电动车行驶里程的关键影响因素。轮胎的胎面一般贡献了轮胎滚阻的50%。稀土顺丁/NdBR是滚阻最低的橡胶,通过使用NdBR和改性溶聚丁苯/FX-SSBR复合白炭黑填料的胎面配方,能为轮胎带来极致的低滚阻,因而带来更长行驶里程。

除此之外,轮胎在长期使用,会逐渐失压而导致轮胎滚动阻力急速上升,从而影响电动车的行驶里程。通过使用阿朗新科优异的卤化丁基橡胶/HIIR来获得杰出的轮胎气密性,从而将失压率降到最低是保证电动车行驶里程的关键。
03
先进制备工艺——深入电池研发
动力电池堪称电动汽车的“心脏”,其能量密度、稳定性、安全性对整车来说至关重要,电池也占据整车相当一部分重量,因此对轻量化提出了越来越硬性的要求。迎合全球电池领域未来几年强势的增长趋势,阿朗新科也在积极投入电池研发。目前,阿朗新科在全球共有两个电池实验室,一个位于中国常州,一个位于德国多马根。
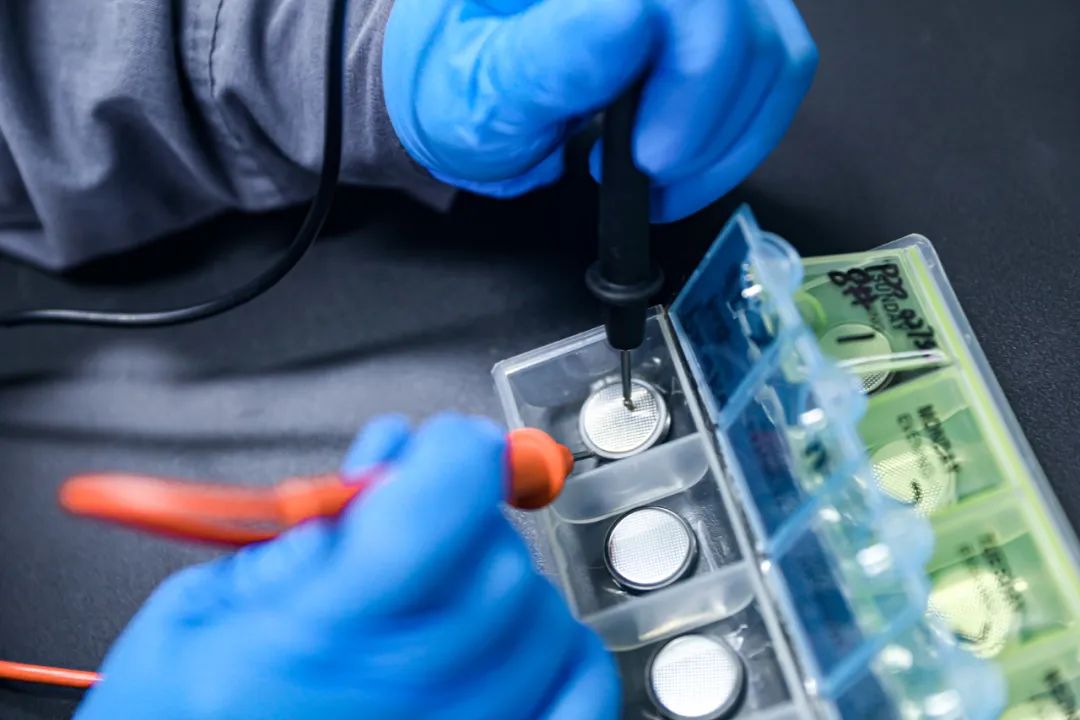
随着阿朗新科常州橡胶技术中心(RTC)全新升级的电池实验室投入使用,公司在汽车电池方面的测试与研究能力将得到大幅提升,可更高效地为客户提供创新服务与轻量化的解决方案。
陈民杰介绍,电池活性材料对水极度敏感,而常州电池实验室具备高度干燥的实验环境(23℃条件下,室内相对湿度在0.1%以下),可保证出色的电池制备和测试能力。在这里,阿朗新科的技术专家们将进行电池浆料的制备和流变性能评估,电池的制备(电池浆料的涂覆、电池的干燥、辊压和切割),以及电池的最终制备和性能评估。尤其是动力电池的轻量化方面,提高电池连接工艺、提高单个电芯的能量密度、采用高容量材料等措施都对电动车减重有一定的帮助。因此阿朗新科也在不断设计、测试并推出创新解决方案。
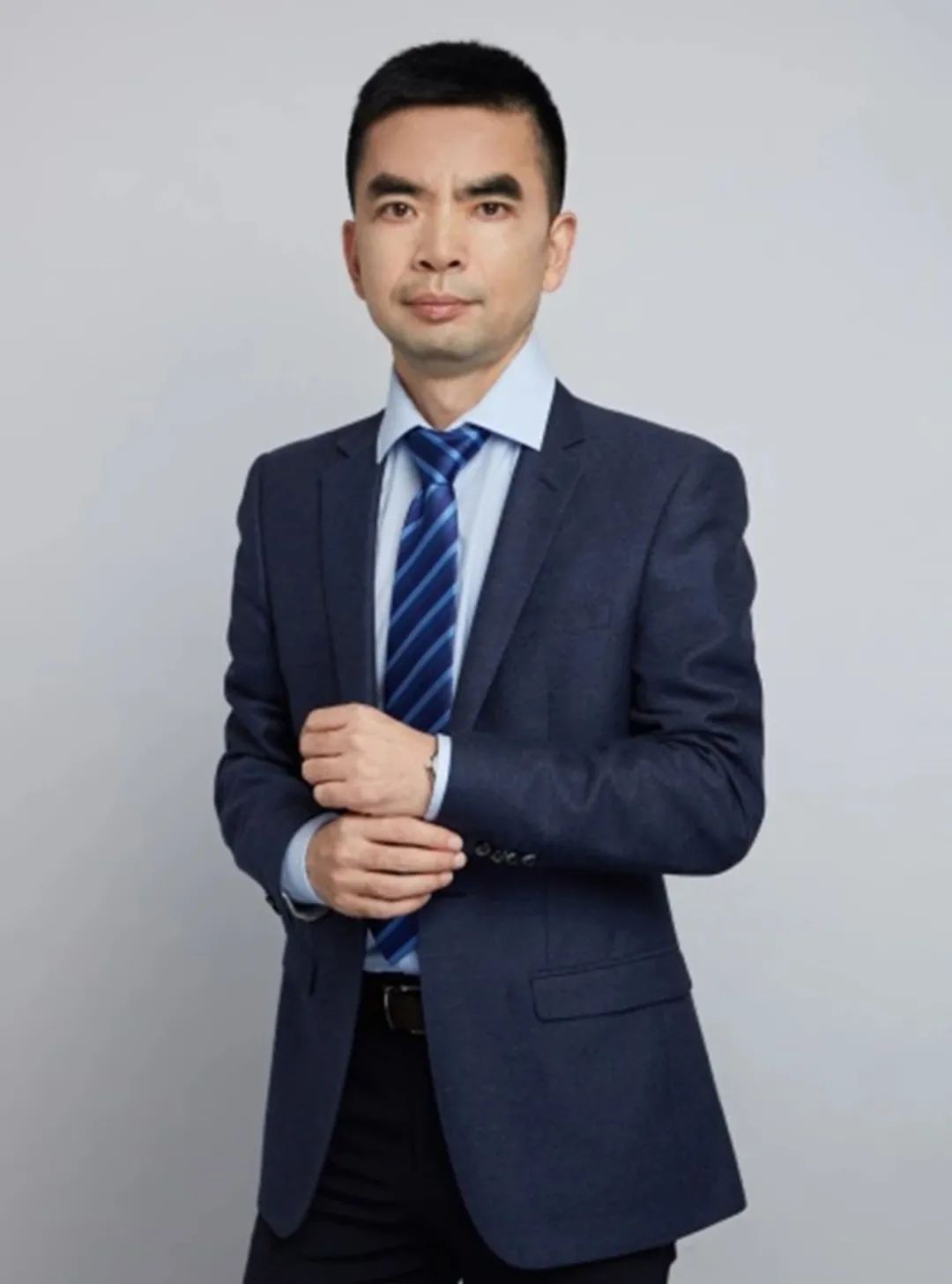
阿朗新科中国技术经理陈民杰博士
04
挑战和机遇并存,中国市场是中坚力量
对于电动化带来的变革,陈民杰坦言,由于燃油发动机的占有率将逐步下降,燃油胶管和耐油密封件的需求将越来越少,这直接影响到NBR和HNBR等耐油橡胶的需求。然而,有挑战的同时,也有机遇。电动汽车的电线使用量大大增加,这给EVM这一无卤阻燃橡胶材料带来机遇。EVM可以替代PVC生产无卤阻燃电线。电动汽车对电池的要求也越来越高,HNBR可用于电池的生产,提高电池性能。
“电动化和智能化还将加速绿色轮胎的推广,同时对轮胎轻量化和低维护提出更高要求,这将推动改性溶聚丁苯橡胶(Fx-SSBR),钕系顺丁(NdBR)和高性能卤化丁基橡胶(HBIIR)更加广泛地使用。”冯伟军补充道。
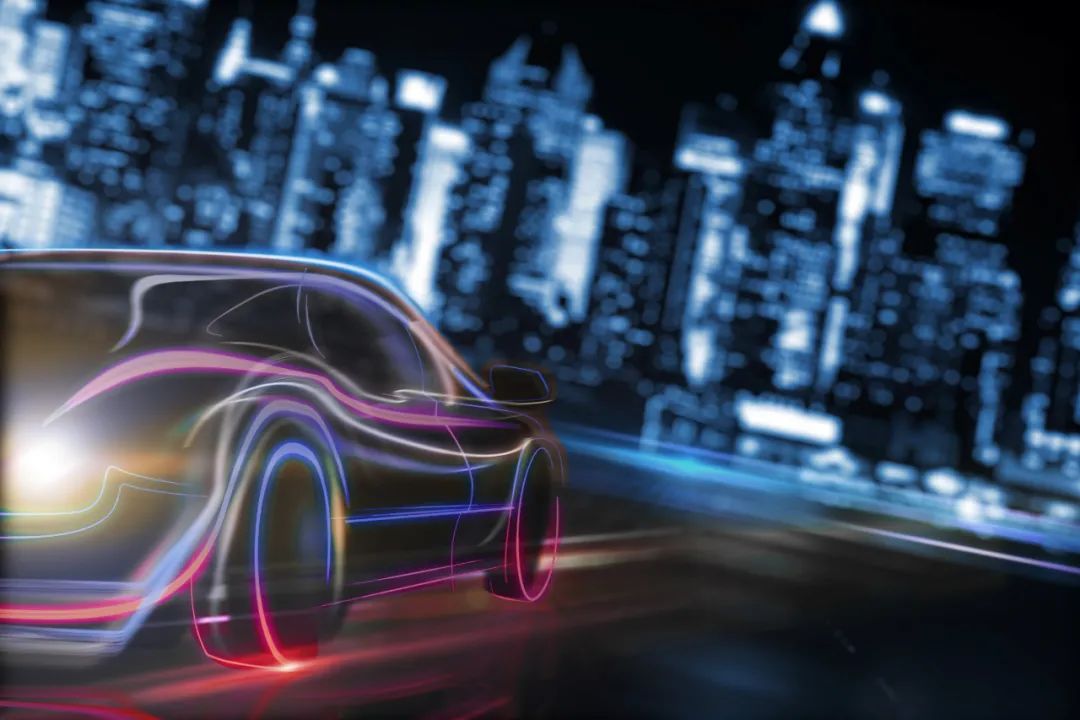
面对电动化带来的挑战和机遇,阿朗新科“与绿色同行”的理念推动公司持续投入研发和创新。尤其中国市场,在阿朗新科的全球布局中占据重要地位。尽管全球经济及橡胶行业正经历各种挑战,中国市场仍然保持稳定。以中国市场为中坚力量的亚太区销量,贡献了阿朗新科超过1/3以上的全球销量。阿朗新科看好中国市场的长期发展,对中国市场的未来增长充满坚定信心。
近年来,阿朗新科加快在中国本土投资建厂的步伐。常州三元乙丙橡胶(EPDM)工厂于2015年正式投产,总投资7.33亿美元,设计产能16万吨;南通丁腈橡胶(NBR)工厂是阿朗新科与台湾台橡集团的合资企业,于2012年正式投产,总投资1.1亿美元,初始年产量为年产3万吨,专注为区域市场提供优质的丁腈橡胶(NBR)。此外,顶尖的橡胶测试中心——阿朗新科橡胶技术中心 (RTC)也坐落于常州EPDM工厂,整合了阿朗新科的橡胶加工与混炼、物理性能测试和化学分析能力,拥有中国目前同类综合性橡胶实验室中最具高科技含量的设备。
结语
电动化浪潮下,电动汽车轻量化会成为未来行业持之以恒的焦点,其具体内容也会随着新技术的出现而不断丰富。作为材料解决方案供应商,阿朗新科的核心使命是通过优质材料改良、结构设计优化和制备工艺革新三大途径,以与时俱进的技术研发和产品创新,满足不断升级的汽车轻量化发展需求。